I think I went a bit over the top in terms of ensuring the join was well pressed together (see photo), but got the desired result.
First, you need to work out what size and design you want.
Then you need to get hold of some plans. Check out the link on the left for B and B yacht designs.

Don't take shortcuts. In these photos, you can see I didn't follow the plans that well. The whole bow including the topsides should have been joined together first. I had a hell of a job getting the topsides to come together evenly.
To be fair on myself, the garage I had borrowed to do the project didn't have enough room to use the method in the plans, (see the link to the left).
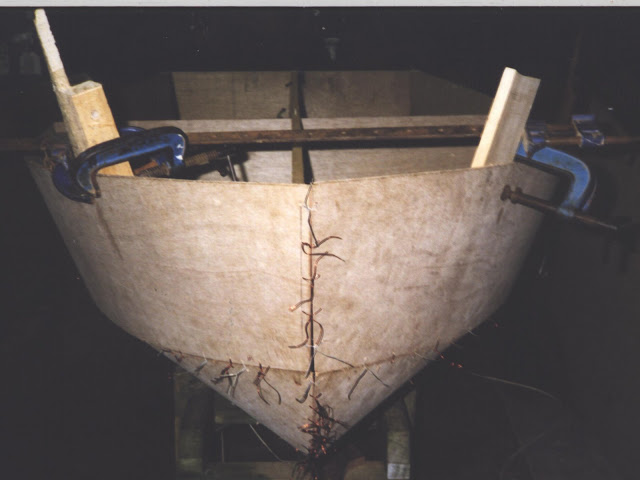
But we got there eventually.
Thank you for inventing the West System Epoxy and fillers for hiding less than perfect workmanship. Who cares about the extra weight.
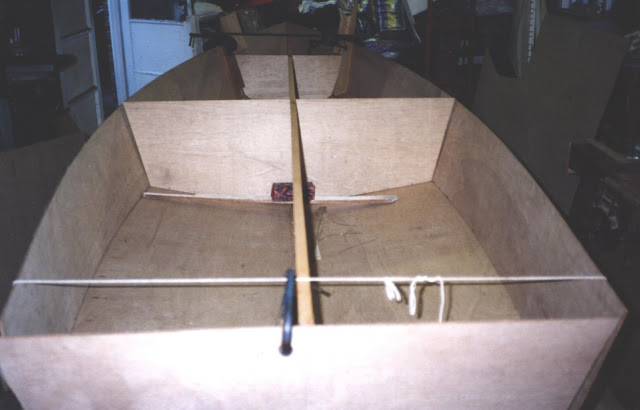
The work progressed steadily over the winter months.
Mostly I worked on it after work in the evening but the weekends were good for achieving so much more. It took up all of my spare time for about four months.
In the weekends the crew would pop around for a while and give a hand with the sanding.

From then on it was lots of filling fairing and sanding. Not the most fun part of the project for me.

A Quick trip to Whangarei on the trailer to make use of my fathers

We used an air spray gun to apply the three shades of two pot paint system from Wairau Paints.

Then we Glued the closed cell foam onto the rubbing strake and covered it with Hypolon strap using Lancer Industries Two Pot contact adhesive.
I was amazed at how much time went into painting and finishing it. Probably about a third of the build time. In part due to the three colours that were each individually masked.
Back to Auckland for "Lawn Trials", which the kids informed me it passed with flying colours.


Fitted in place for offshore passages in the nested position the 11 foot long boat only took up 6 foot deck space. Nice and snug.

It is a favourite pastime for Hamish to go for a blat around the bay. Seen here with a five hourse Yamaha. It is super quick with the new eight hourse Yamaha.
It sails well. I used a full laser rig but have puchased a laser radial rig for when the wind is up a bit. It floats high and leaves most of the water outside the boat when righted after a capsize. It planes like a skiff when the wind is up, great fun.
And it tows really well, even in a chop.

We got what we wanted in a dinghy. It is a bit of a pain having to put it all together and stow it when the weather is expected to be less than ideal and we are passaging. This is nothing in comparrison to having a tender that is as versitile as our Spindrift 11 Nesting Dinghy. We named her "MyST" (My Spare Time).